Introduction to Fujikura Composite Shafts
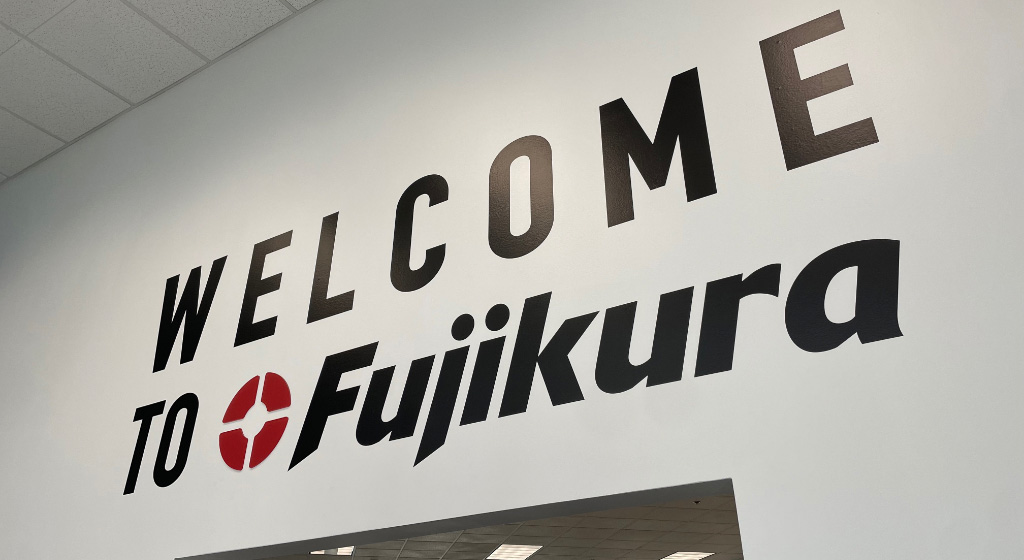
Fujikura began its production of graphite golf shafts in 1974. Since that time, there have been significant advancements and changes in graphite shaft design and development. Types of materials used, material integration, measurement, and overall design concepts have all evolved significantly over the years, continually setting new standards for product and player performance.
Graphite Shaft Evolution
In the beginning, graphite shafts were not designed with the parameters of balance and consistency we expect today. Graphite materials have always been wrapped with a high level of precision and accuracy, but the final products often lacked concentricity. Now, our understanding of the unique geometry required to create products that target specific performance attributes allows us to continually innovate and produce the world’s best performance golf shafts.
Early graphite shafts were often designed and built utilizing a small number of large sized plies (sheets/pieces of material) and limited to only a couple of material types. These plies were then wrapped several times to create greater stiffness in a particular area. While these designs were initially conceived to have the similar performance characteristics of steel, it also limited the overall design and performance in that if any one part of the shaft’s geometry changed, another part changed with it.
With the design evolution of increasing the number of plies and broadening the array of materials used, we’re now able to conceive and produce much more intricate and precise layouts. Overall, we’re equipped with a much better understanding of how material applications can drive shaft performance, leading to a more superior product.
Piece of the Puzzle
As a component of a finished golf club, shaft design also evolves alongside golf club design. Changes in clubhead weight, clubhead center of gravity location, and changes to “standard” club length have all required tweaks to the shaft’s balance point to achieve correct swingweight targets. Torque has also become a much more widely focused on and addressed performance metric, especially in premium and more complex shaft designs. Original “low-torque” designs required larger amounts of material in the mid and tip sections, which added to the product’s overall weight. The evolution of lightweight composites has helped create high-performance, low-torque products that can be made in almost any weight configuration.
Aside from graphite wood shaft evolution, graphite iron shafts have also improved dramatically compared to early offerings. Initial graphite iron shafts required club builders to build each iron .5” over-length or add significant weight to the head to try and achieve a proper swingweight. Now, technologies like our HDCC (High Density Composite Core) and MCT (Metal Composite Technology) enable us to appropriately add weight in specific sections of the shaft to achieve correct swingweights.
Additionally, technological advancements in the wood shafts can now be applied to iron shafts as well to offer players exceptional gains in stability, accuracy, and overall performance. Graphite iron shafts are now also offered in variety of heavier and stiffer options as opposed to only lighter and softer flexes, helping graphite appeal to an entirely new skill set and player types.